ABZ Asphalt Plant
The first asphalt road was built in ancient Rome, from natural asphalt heavy oil and bitumen Asphalt plant XXI CENTURY At the heart of the plant laid new technical solutions, allowing for significant energy savings and to guarantee the high quality concrete mix. Main technical characteristics: 1. Technical performance (with humidity up to 7%), m / h 60.0 2. Mixer: - Type - Continuous; - Mixing time, with 90-120 3. Dosing material: weigher continuous 4. Dust collectors - bag filters. 5. Consumption of diesel fuel (gas) per 1 ton of finished mixture, kg / ton (m3 / t) - If the initial material moisture 3% 4.4 (5.4) - If the initial material moisture 5% 5.4 (6,64) - If the initial material moisture 7% 6.77 (8.3) 6. The volume of bunkers aggregates (aggregate supply), m3 4x8, 0 = 32.0 - An additional tank, m3 1x8, 0 7. The volume of bitumen, m3 to 30,0 8. Volume of the warehouse (silos) of mineral powder, 25.0 m3 9. Hopper capacity of the unit ready mix, 65.0 m 10. Installed power, kW 210 11. Supply voltage and frequency of 380 V/50 Hz 12. Number of staff (operator) 1 Technical feature of the plant is that an increase in material moisture capacity of the plant does not change. System consists of: ABZ consists of the following units: 1 - power supply unit. Suitable for receiving and filing (dosage) of mineral materials (sand, gravel); 2 - furnace-dryer unit. Intended for drying and heating of mineral materials; 3 - unit sorting and batching. Intended for the division of mineral material into fractions 0,16-1,25 mm, 1,25-5,0 mm and 5.0 mm, storage and dispensing of these fractions into the mixer; 4 - mixing plant. Designed for mixing asphalt; 5 - unit preparation and filing of bitumen. Designed for storage, dosing and feeding into the mixer foamed bitumen; 6 - gas treatment unit. Intended for abstraction of the dryer flue gas dust, dusting, separation of coarse and fine dust, supply of filtered heated air drying or heating units ABZ; 7 - aggregate of mineral powder. Designed for storage, dispensing and supply of mineral powder in a mixer; 8 - ready mix plant. Designed for storage, dispensing and delivery of finished asphalt for shipment in the cars; 9 - Control Room Additional equipment of ABZ Asphalt Plant: 1 - aggregate supply of flour components. Designed for storage and feeding (dosage) of dust; 2 - unit of storage and filing frezezha, fiber, etc.; 3 - unit of storage and filing him.dobavok (SAW WSP ...). At Concrete Plant a new generation is used as a dryer, instead of the drum unit vibrokipyaschego layer that allows us to obtain significant savings in fuel for drying and heating of mineral materials. Thus there is a number of features that tumble dryer is not implemented. First is the use of a two-zone hot air outlet and return it to the drying process, as well as other heating units. Second, clean the surface of the mineral material (dust removal), which is essential for obtaining high-quality concrete mix. In addition, the organization of the gas cleaning system allows you to split an action taken by the dust on a large (0,071-0,16 mm) and small (less than 0.071 mm). No less significant contribution to improving the quality of preparation of concrete mix is to use a new ABZ original mixer, which is a 2-Valenod continuous mixer with separate loading of materials and injection of bitumen. In purified (dust-free) material initially introduced foamed bitumen for better adhesion to the surface of the material particles, then (as the movement of material in the mixer) is introduced mineral powder or dust entrainment in the third zone is introduced bulk bitumen for the final mixing. Mineral powder and dust are introduced with a screw feeder, which minimizes the removal of material from the mixer. Dosage and commissioning of mineral powder and mixing the two fractions of dust (coarse and fine) is carried out feeders, feeders from separate mixers that optimally expend mineral powder, replacing him with petty fraction of dust removal. Using a continuous mixer allows mixture was stirred for 80-90 seconds, which is optimal for generating a mixture with the highest strength characteristics. According Soyuzdornii increase the mixing time to 90 seconds can increase the performance of mechanical strength of asphalt concrete by 25-30%. In this case, continuous mixer can not reduce the overall performance of the production of asphalt due to increased mixing time. Another important innovation in ABZ is the classification of sand with vibroshock rumble , ensuring high efficiency of the classification of material and self-cleaning screens, which allows the classification of the material into classes 0,16-1,25 mm, 1,25-5,0 mm. The effect of self-cleaning screens is very important to stabilize the quality of screening, as in the screening of fine-grained material containing grains of acicular flakiness and shape of the cell screens clogged, reducing the surface of the living section of screens, which leads to significant clogging of the upper (oversize) the lower grade material, and change in the sieving curve of this fraction. Application vibroshock rumble for the classification of grain screenings 1,25 mm, not only prevents clogging holes sieve (screen shake on impact and cleaned), but also provide improved performance of the screening. New Asphalt and Concrete can be equipped in order to ensure the quality of asphalt mixtures based on a fully optimized particle size distribution, granulometry for continuous monitoring of particle size distribution of small filling (sand, dust, ash ...), that can automatically adjust the operation of mineral feeders materials, and, if necessary, the dosage of bitumen. Temperature controller and the viscosity of bitumen is fed into the mixer, which works well in automatic mode, can not only provide the necessary parameters of bitumen, but also save on heating of bitumen.
Relative FAQ
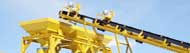
Email: sales@bossbuyer.com
Skype: bossbuyer
Market Hotline
0086-21-61435-919
Service Hotline:
0086-21-61435-919