Design and Optimisation of Crane Jibs for Forklift Trucks
The objective of this paper is to present a new methodology of calculation by means of the F.E.M. applied to crane jibs. This analysis has been carried out in terms of strength and stiffness, and for any type of crane jib: telescopic crane, lattice crane, closed beam crane, etc.
There have been simulated different load cases and boundary conditions that the structure should bear. This load cases can be obtained from normal and extreme operation of the crane, and there have been taken into account current regulations and previous experience.
It has been also necessary to define the methodology to simulate non structural elements, contacts, materials, etc. Concerning regulations, it has been necessary to make an adaptation of the regulation UNE-58536, because the specific regulation affecting these crane jibs (UNE 1726), was not enough restrictive. Moreover it has been necessary to estimate some translational and rotational velocities to apply the regulation.
Furthermore, the welding of some parts has been simulated and analyzed, and it has been carried out a comparative analysis between the experimental results and the numerical results for some load cases. Once this correlation has been obtained the methodology of calculation and the numerical results are validated.
The article presents a methodology for the design and optimization of crane jib for manipulative telescopic using the finite elements method. For it, the design attends both to stiffness, strain, weight and regulation criterions and it is possible to apply to all types of crane jibs: telescopic (where the dynamic effects are relevant), in lattice, closed box, etc. The start point of the analysis is the UNE-58536 standard because the 1726 one is insufficient and slightly restrictive for the calculation; it has been necessary to estimate some speeds.
From these standards and the previous experience of the manufacturer there have been established the cases of load and contour conditions, both for habitual use and for extreme use and they have defined the materials, the contacts between pieces, the welds, etc.
To check this regulation it has been applied to two types of crane jibs, a telescopic and a closed box one, which later have been optimized using numerical technologies and finally the telescopic jib has been tested using extensometrical procedures in order to check the numerical results and the methodology of design.
The principal conclusions that are obtained are that it has been developed a methodology for the design, calculation and optimization of crane jibs for fork-lift trucks, adapting the regulation UNE-58536 for movile cranes, becouse the norm UNE-1726 is not too much restrictive; so it was necessary to define the load cases, the boundary conditions, the loads, the materials, the welds models, etc.
Furthermore some additional load cases not contemplated in the norm have been established and they have a great interest for a correct designo of the mechanical set, principally because the simulate some maneuvers that, although they are dissuaded or prohibited, can happen during the use of the crane jib.
Also a calculus methodology has been established using numerical technologies, especially finite elements method (F.E.M.), that allows to simulate perfectly all the elements and welds of the mechanical set and simulate all the load cases, and visualize in every point the stress, the strain, the displacements, etc.
On the other hand there has been checked the numerical results using extenosmetrical methods, obtaining a high degree of correlation and a low deviation (less than 12 %) that allows to validate the numerical results and the calculus methodology.
Relative FAQ
- Testing and Examination of Cranes and Certain Lifting Appliances
- Construction and Maintenance of Cranes and Lifting Appliances
- Classification of Crane Anti-sway devices
- Cranes, lifting appliances and fork lift trucks
- Cranes and hoists operating rules, Crane operating rules, Hoist operating rules
- Gantry Crane or Goliath Crane
- What is crane certification? How often does a crane have to be certified?
- Concrete Mixing Transportation Truck
- Factors behind the selection of construction equipments
- Wind and Tower Cranes
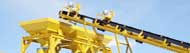
- Forklift truck
- Water and Oxygen Jet Machine
- Concrete Pump Truck
- Mobile Crushing Station
- Dedusting & ash conveying
- Diode laser equipment
- Semi-Mobile Crushing Plant
- Fire Rated Steel Door
- Gas Tight Doors
- EOT Crane
- E-energy Breast Beautifying Laser
- Pulse bag dust collector
- Broaching machine
- Long Pulse ND:YAG Laser
- Air box pulse dust collector
Email: sales@bossbuyer.com
Skype: bossbuyer
Market Hotline
0086-21-61435-919
Service Hotline:
0086-21-61435-919