SCREW CONVEYORS
Screw conveyors are conveyor systems that transport bulk materials from one location to another. In certain applications, screw conveyors may also prove advantageous in the breakdown and agitation of materials. Screw conveyors consist of a rotating, spiral screw within a trough. The rotation of the screw pushes the materials through the trough to the intended destination. Screw configuration make screw conveyors useful in transferring powders, sludge, fuels, ash, feed, cement, ice and certain minerals. Because the screw will cut through materials during operation, sticky materials, materials that do not breakdown easily, or those materials not intended to be broken down are usually not ideal materials for screw conveyor systems to process.
INTRODUCTION of SCREW CONVEYORS
Screw conveyors are found in numerous industrial applications in the agricultural, food and beverage processing, pharmaceutical, chemical, mining, oil and gas, and construction industries. Screw conveyors are cost-effective and easy to install. The selection of a screw conveyor depends upon the industrial application; material and material consistency; and additional operations required of the screw conveyor system.
Consists of a tube or U-shaped stationery trough through which a shaft-mounted helix revolves to push loose material forward in a horizontal or inclined direction and a drive unit for running the shaft.
Screw conveyors are accepted in most industries as the usual means of conveying powders and granules from point 'A' to point 'B'. Designs can be applied to most applications in the food, pharmaceutical, chemical, mineral and sewage treatment industries.
Compact in design, screw conveyors are easily adapted to suit the needs of the location and can be mounted horizontally, vertically or at an angle, and include planes as necessary.
Machines are available in trough or tubular form; trough conveyors are generally used in horizontal applications and at inclines up to 200, while tubular conveyors are selected for elevating purposes at angles greater than 20.
Screw conveyors are very versatile in that as well as conveying they can be used as feeders and to control material flow in processing operations, and also as mixers, agitators or stirrers within a variety of processes. Screw conveyors can be sealed to prevent leakage, can be jacketed to provide a drying or cooling medium and can be manufactured in special steels to resist corrosion, abrasion or high temperatures.
Screw conveyors serve the manufacturing industry in a wide variety of applications : conveying, distributing, collecting, mixing, heating, cooling, elevating, batching, blending, aerating and providing crystallization or coagulant action.
Screw conveyors are used principally for transmitting material in the form of powder or paste with the application of rotating screw.
Flourmill industry was probable the first to employ horizontal screw conveyors to convey corn and flour. These screws were made by fitting wood blades to a central shaft rotating inside a cylindrical casing. Even now such screw conveyor enjoys popularity in agrobased industries, handling grains and flours, because of low friction, negligible cohesive strength of the material.
The material is moved forward along the axis of the trough by the thrust of screw thread or flight. A helical blade is attached to a drive shaft which is coupled to a drive unit. The shaft is supported by two end bearings and intermediate bearings. The U-shaped trough has a cover plate with a opening for lading the conveyor. A discharge opening is provided at the bottom of the trough. The loading and discharging points can be located anywhere along the trough. More than one feed hopper and discharge hopper may be fitted according to the necessity.
The principle of material movement along the trough is similar to the sliding motion of a nut along a rotating screw when the nut is not allowed to rotate. The weight of the material and the friction of the material against the wall prevent the load from rotating with the screw.
ESSENTIAL COMPONENTS
The Crmrsyor Some imparts a smooth positive motion to the material as it rotates within the trough.
Couplings and Shag connect and transmit motion to subsequent screw conveyors. Held in place by self-locking Through-U-lockbolts.
Hangers provide support, maintain alignment and serve as bearing surfaces. Troughs and Convtyors completely enclose the material being conveyed and the rotating parts. Covers are available in various types and are secured to the trough by Spring, Screw, Tight-Seal or quick-acting Barron Clamps depending on the trough being used.
Inter and Disdrarge Crxrrings may be located wherever needed, discharge spouts may be without slides or fitted with either flat or curved slides. These slides may be operated by hand, rack and pinion gears or by power.
TYPES OF SCREW CONVEYORS
- Flexible screw conveyors move solids and powders in all directions. Flexible conveyor systems contain a flexible screw capable of self-centering itself within the conveyor tube, which prevents scraping of the screw against the tube wall. Because the conveyor motor powers the screw directly, the need for extra components is eliminated, reducing upkeep and maintenance and increasing cost-effectiveness.
- Jacketed screw conveyors use substances such as water, oil, or steam to provide heating or cooling to materials transported through a screw conveyor. Jacketed screw conveyors consist of an enclosure surrounding the conveyor trough.
- Portable screw conveyors can be transported from one location to another, which increases convenience and the efficiency of the industrial application.
- Trough screw conveyors are common in the food processing industry. Trough conveyors contain an open channel duct through which the materials are conveyed.
- Tubular screw conveyors protect against material contamination during conveyance, which remains advantageous in industrial applications involving sensitive materials. Tubular screw conveyors consist of an enclosed tube-shaped duct through which the materials are conveyed configuration may take cleaning difficult.
TYPES of SCREW FLIGHT
The screw of the conveyor may be right-hand or left-hand, the right-hand type being the usual design. The threads of the screw may be single, double or triple.
The flight of the screws may be made in either of the two ways : (a) as helicoids, (b) as sectional flight. (a) Helicoid flight are formed from a flat bar or strip into an edge. (b) Sectional flights are formed from a flat disc and the thickness of the thread is uniform throughout. A continuous helot is made by joining a number of sectional flights together on a piece of pipe and butt-welding them. Various styles of screw flights are in use, depending on the service required:
(a) Single Flight Standard Pitch : Conveyor screws with pitch spacing equal to the diameter are considered standard and arc suitable for most conveyors of conventional horizontal design.
Flights with pitch progressively increased are used to draw fine, free flowing materials uniformly from the entire length of the feed opening.
(b) Single Tapered Flight Standard Pitch : Tapering flight screws are generally recommended to draw friable lumpy materials from bins or hoppers.
(c) Double Flight Standard Pitch : Double flight produce a smooth gentle flow of certain materials are recommended for augers or post hole digging and similar applications.
(d) Short Pitch or Continuous Flight : If the conveyor is required to handle dry granular or powered material that do not pack, this style of flight may be selected. It is of regular construction and recommended for inclined conveyors having a slope of 20 degrees or more, including vertical conveyors. This style is extensively used feeder screw. Short pitch screws are recommended for inclines over 20 degrees slope to vertical conveying. They retard flushing of free flowing materials.
(e) Half pitch conveyors are recommended for inclined or vertical conveying and for materials which are very free Rowing.
(f) Ribbon Flight : If the conveyor is to handle lumpy, clinging, sticky, gummy or viscous substances, this type flight may be selected. It consists of continuous helical flight formed from steel bar and secured to the pipe by supporting lugs. Ribbon flights are excellent for sticky or gummy materials where the gap between the screw and the pipe prevents material build-up.
(g) Cut Flight : In this type of flight screws have notches cut in the periphery of the flight. These notches supplement the conveying with moderate mixing action. They are recommended for conveyors required to handle light, fine, granular or flaky materials. The screw flight periphery is notched to supplement the conveying action with a moderate mixing action.
(h) Cut and Folded Flight : This type of flight is characterized by notches as in cut flight, together with folded segments. This type of flight creates agitation and aeration resulting in better mixing. This type of flight is used to handle light or medium weight materials having fine, granular or flaky characteristic.
(i) Some screw conveyors have cut flight with paddles mounted at regular intervals. The flow of material past the flight resulting in greater agitation and mixing. The paddle conveyor is made of steel paddles on threaded rod shanks inserted through the pipe. Conveying action can be controlled by adjusting the paddle angle. Excellent for stirring, blending or dry or fluid materials.
(j) Sometimes screws are made of stainless steel to suit special requirements, like the sanitation requirements for handling foods, drugs and other hygienic materials.
FEED AND DISCHARGE ARRANGEMENTS
Feeding and discharging hoppers may be placed conveniently along the length of the conveyor the various possible configuration. According to necessity any arrangement may be adopted.
STANDARD DIMENSIONS of A SCREW CONVEYOR
Screw conveyors are usually designed and manufactured with standard dimensions of nominal diameter of the helical screw, pitch of screw, diameter of screw shaft, height of the conveyor above the centre of screw and thickness of trough. In this regard usually IS : 5563-1985 is followed.
Effect OF Lump Size
The size of a screw conveyor depends on two factors : (i) The capacity of the conveyor and, (ii) The lump size of the material to be conveyed. The size of the lump indicates the maximum dimension of the particle.
Usually there are three ranges of lump sizes which are considered for selection of screw size. These are :
1. A mixture of lumps and fines in which not more than 10% are lumps ranging from maximum size to one half of the maximum; and 90% are lumps smaller than one half of maximum size.
2. A mixture of lump and fines in which not more than 25% are lumps ranging from the maximum size to one half of the maximum; and 75% are lumps smaller than one half of the maximum size.
3. A mixture of lump only in which 95% or more are lumps ranging from maximum size; and 5% or less are lumps less than one tenth of the maximum size.
The allowable size of a lump in a screw conveyor is a function of the radial clearance between the outside diameter of the central pipe and the radius of the inside of the screw trough, as well as the proportion of the lumps in the mixture.The lump size of the material affects the selection of screw diameter D, which should be at least 12 times larger than the lump size of a sized material and four time larger than the largest lumps of an unsized material.
ADVANTAGES OF SCREW CONVEYOR
The screw conveyor is one of the most cost-effective methods for transporting bulk materials. Screw conveyors are used in thousands of applications in almost every industry. The screw conveyor has many advantages over other types of bulk material handling equipment. Some of the advantages are :
(a) Screw conveyors are capable of handling a great variety of bulk materials from sluggish to free flowing.
(b) Screw conveyors can have multiple inlet and discharge points. Bulk materials can be conveyed and distributed to various locations as required. Slide gates or valves can be added to control the flow into and out of a screw conveyor.
(c) When a screw conveyor is used as a metering device, it is considered a screw feeder. Screw feeders are used to initiate a material process by metering product from a bin or hopper.
(d) Screw conveyors are very compact and adaptable to congested locations. Screw conveyors do not have a return similar to a belt or drag conveyor.
(e) Screw conveyors are totally enclosed to contain the product and prevent spillage.
(f) Screw conveyors can be utilized in the horizontal, vertical or any inclined position depending upon the characteristics of the product being conveyed.
(g) Screw conveyors can be used for mixing various products together and for breaking up large lumps.
(h) Screw conveyors can be designed without a centre pipe This type of conveyor is called a shaft less screw conveyor and is designed for conveying wet, sticky, sluggish products such as industrial sludge and bio-solids.
(i) Screw conveyors can be used to cool, heat or dry products in transit. Depending on the heal transfer requirements, a screw conveyor can be jacketed, or a hollow-flight design utilized to provide the necessary heat transfer for the application.
(j) Screw conveyors can be designed to be vapour-tight or hold an internal pressure. This is very important when conveying toxic or hazardous products such as those in the chemical industry.
(k) Screw conveyors can provide an air lock between upstream and downstream equipment.
SCREW CONVEYOR CHOICE
Determining the most efficient method to move material from point A to point B is a matter of simple deduction. Just match the material flow characteristic, process parameters and space limitations to the performance windows and dimensional restrictions of different conveyors. Then, factor in purchase, maintenance, labour and cleaning costs and the conveyor choice is clear.
Because the performance, size and cost of conveying methods vary, only a general knowledge of the different types is necessary to decide which is best. Armed only with the fundamentals, anyone can determine whether or not a flexible screw conveyor can handle an application most efficiently. In its basic form, a flexible screw conveyor consists of a spring-steel or stainless-steel, flexible screw that is enclosed in a flexible or rigid steel tube. A small-diameter, plastic inner tube may also run the length of the screw. The conveyor is driven by an electric motor normally located at the discharge end.
The intake end of the conveyor tube is typically equipped with a charging adapter. This U-shaped trough connects to the cutlet of a hopper or directly to the outlet of process equipment such as a bulk bag discharge, bag dump station, grinder, crusher, screen, blender, reactor or storage vessel of any kind.
The flexible screw passes through the charging adapter trough, exposing a section of the screw to material flowing into the trough from above. When rotating, the exposed section of screw feeds material into the outer tube. It is then propelled through the tube by the enclosed portion of the screw. Because of its loose fit, the screw automatically selfcenters within a material-filled tube, providing clearance between the screw and tube wall. This clearance between the screw and tube wall can eliminate or minimize grinding, crushing and impact damage.
LIMITATIONS OF SCREW CONVEYOR
Because every conveying possesses has inherent limitations, each must be identified and ruled unimportant or less important than corresponding attributes, before deeming a flexible screw conveyor to be the best alternative for an application.
(a) Screw conveyors, like other mechanical conveyors, do not generally evacuate material completely when operating in a forward direction. Residual material can be fully evacuated, however, by removing the cleanout cap and reversing the screw rotation.
(b) Although these conveyors tend not to grind or crush, not all materials can be conveyed damage-free. Some large, brittle flakes or large, soft particles may break, particularly through long runs or steep inclines in a flexible screw conveyor. But, proper system engineering can eliminate or minimize these effects.
(c) Flexible screw conveyors are often used where capacity requirements are less than 50 tph (per conveyor). Thus they are infrequently employed for off-loading of ships or railcars.
(d) Screw conveyors do not always get favorable consideration due to high friction of the material against screw and trough, probability of material degradation due to crushing of material and due to higher power consumption resulting from higher friction. Therefore, screw conveyors have limitation in capacity and distance of conveying. They are suitable for low and medium capacities for short distance. Capacity may be as high as 100 m3/hr and distance of conveying is of the order of 30 to 40 m typically.
APPLICATIONS op SCREW CONVEYORS
(a) Screw conveyors are employed for handling a great variety of materials, which have relatively good flow ability. Sticky and stingy materials are unsuitable for screw conveying.
(b) Dusty, hot materials, or materials having ordour arc often conveyed by screw conveyors, because, it can be easily made dust-proof by jacketing the trough.
(c) Typical applications include grain storage plants, feed mills, cereal processing plants, chemical plants, sand preparation shop of a foundary for delivery of clay to the mixing machines.
(d) Screw conveyors arc very suitable for being adopted as a device to control the volume of materials flow from the bottom of bins, hoppers, storage silos etc. When screw conveyors are used for this purpose they are termed as screw feeders. Screw feeders have wide applications for the operation of processing units, like driers, hammer mills, oil expellers and other innumerable mills.
(e) Screw conveyors may be used to convey materials which can be subjected to thermal operation during transit. The conveyor trough is provided with jacket through which the heating or cooling medium may be circulated to effect the thermal operation.
(f) Screw conveyors are sometimes used for blending of several ingredients to prepare a finished products. The screw profile of the conveyor are specially designed for this purpose.
(g) Conveying between storage vessels.
(h) Bulk bag dischargers.
(i) Manual bag dump stations.
(j) Drum dump stations.
(k) Cnisbers, screen= and blenders.
(l) Reactors and packaging equipment.
(m) Injection molding and extrusion machines.
(n) All industries in particular mining, food, chemical, paper and pulp, waste, building, wine, power generation etc.
(o) Controlling material from the bottom of bins, hoppers of the like.
Relative FAQ
- TYPES OF BELT CONVEYORS
- ESSENTIAL COMPONENTS OF BELT CONVEYORS
- BELT CONVEYORS, INTRODUCTION TO BELT CONVEYOR
- MOBILE CRANES INTRODUCTION
- CRANE OPERATORS AND OPERATIONS QUALIFICATIONS
- CLASSIFICATION OF CONSTRUCTION EQUIPMENTS
- Self-Raising Tower Crane
- Crawler Crane QUY50
- Safe Crane Operations
- Safety Rules for Construction Site Workers
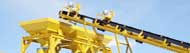
Email: sales@bossbuyer.com
Skype: bossbuyer
Market Hotline
0086-21-61435-919
Service Hotline:
0086-21-61435-919