Hydraulic Telescoping Gantries
Telescophig gantries are typically used for heavy lifting where mobile cranes or derricks are not feasible, where classic "jack and slide" procedures are awkward, or where other conditions make use of the gantry the most economical means to perform the work required. These systems first came into regular use for rigging during the early 1980s.
Characteristics of hydraulic gantries are different from those of other rigging equipment. Cranes will fail without warning when structurally overloaded to the limit. Gantries, on the other hand, can be made to refuse excessive loads by control of hydraulic pressure. But gantries can be sensitive to inadequacies in the strength, levelness, stiffness, or arrangement of their support structures and require much more deliberate attention to support than cranes do. Close engineering scrutiny of ground support is seldom needed for mobile cranes; for gantries it is the general rule.
There are two basic types of hydraulic telescoping gantries. Both types work in groups of two or four jacks. Each jacking unit is made up of a wheeled structural box on which one or two hydraulic cylinders are mounted. A steel header beam is fitted across each pair of jacking units. In a typical operation, loads to be lifted are suspended from these beams by slings attached to lifting link yokes over the header (Figure 2.50). The assembly can be used in place for lifting, or can be made to travel along steel runway beams or on steel plates over concrete.
The original and most common type of telescopic gantry utilizes large diameter multistage lift cylinders with as many as five stages and fully extended height of as much as 45 ft (13.7 m). The capacity for a pair of units can be 1000 tons (900 t) or more, but the capacity reduces with cylinder extension. The stages sequentially extend with the smallest diameter, and hence the weakest stage at the top. The lifting ability, structural strength, and structural stability of gantry legs depend entirely on the cylinders. Because lateral strength is limited by these cylinders behaving as a cantilevered column, the system is sensitive to side loading Load pendulation, out of levelness, and side-pull from rigging operations can cause side loading.
The second type of hydraulic telescoping gantry was developed to reduce sensitivity to side loading. These units have a single cylinder at each jacking unit, but the cylinder is enclosed in and braced by a telescoping steel box structure called a left lxxxn (Figure 2,51 ). The stout boom all but eliminates the threat of structural failure from side loading, but it does not make the gantry immune to overturning. Exposure to the overturning hazard can occur from side pull while tripping a load, particularly when there is not much vertical load acting to stabilize a unit. Ordinarily two pairs ofjacks are used for tripping; the operation must be carefully controlled to mitigate side loading. When a single pair is used, holdback lines are needed to restrain against overturning.
Gantry legs interact with one another. In the direction perpendicular to travel, the header beams dictate that lateral movement at the top of one leg must be exactly matched by movement in its partner. Similarly, the weight and rigidity of the load can cause the tops of the legs in the second pair ofjacking units to move in response to movement in the first pair.
Once a load is lifted, a gantry system can be used to travel laterally with the load before lowering. Travel along the track is referred to as a propel movement. Lateral shifting can also be accomplished by rolling or sliding the lift links along the header beam. When pulling is done from outside, there is side loading that must be counteracted using opposing guys or other means.
Two tandem pairs of telescopic gantries are sometimes used to carry a load placed atop the header beams. The higher the load center of gravity is above its base in comparison to base width, the more care is needed to keep the load level to avoid tipping or uneven distribution of loading among the lift cylinders.
For boom-type gantries, clearance and wear at slider pads is inelegantly referred to as slop and the lateral displacement it causes at the top of the vertical boom is called drift. Aside from slop, there are several possible causes for lateral displacement at the tops of gantry jacking units, but displacement from out-of-level supports can be the largest. The entire gantry structure is affected by the levelness at each of thejacking units. Firm and level track support is crucial, and the tracks themselves should be designed to deflect very little under load.
When the top of ajacking unit moves with respect to its dead plumb position, the wheels supporting that jacking unit are no longer uniformly loaded, there are reactions at the wheels, which change to counterbalance the shift at the top. Movement at the top indicates that the load has also moved, and that each unit will no longer be subjected to its original share of load weight. Track beams must be capable of accommodating this reallocation of forces. The gantry structure relies on the track beams for support of its individual wheels and to maintain the entire structure plumb and steady as the gantry travels.
The base of each jacking unit is typically furnished with eight steel wheels, two pair on each side, and two track beams are typically used on each side of a gantry set up when travel is contemplated. Pairs of wheels are centered on the track beams; a steel bar is welded to the beams in the space between paired wheels to keep the wheels centered. Some support conditions can be referred to as "hard points." A hard point is a support point, that is, for practical purposes, nonyielding, or incapable of meaningful displacement. Examples of hard points would be solid rock, a substantial concrete mass, or steel bolsters which are in turn supported on a hard point. Any other support material will displace either elastically or permanently, the amount of displacement varying with the material. Natural wood or plywood displaces elastically at low loading levels and permanently at high levels. Soil displacement has both elastic and permanent components, and those components can vary with the nature of the soil, degree of compaction, and/or the moisture content of the soil. Soil displacement, or settlement, is time dependent, part of the settlement takes place immediately and the remainder as time progresses.
Displacement at any point along a track beam is the algebraic sum of the support medium displacement, track global displacement, and local wheel displacement. The track beam design process must substantiate that the differential displacements that will inevitably take place along the track beam or pair of beams are within tolerances that will not be detrimental to gantry operation and safety.
At any one point, a track beam which has initially been set level can go out of level when loaded if the shims at one or more support points are looser, thicker, or of different material than the adjacent shims, or if the supporting material is of a yielding nature with respect to the support of the adjacent track beam.
The centering of the load, with respect to thejacking units, affects the distribution of load among the units and thus can affect lean. Likewise, if one header beam is permitted to go out of level, the "table leg effect" would cause a redistribution of loading. This is similar to a four-legged table on a hard floor. The table will rock and will be, in essence, supported on two diagonally opposite legs. In like manner, when onejacking unit is extended more than its partner, it and the diagonally opposite unit would try to carry the entire load-the equivalent to a rocking table. In actuality, thosejacking units will tend to carry less than the full load because of the limited hydraulic pressure available and elastic effects, including the stretching of wire-rope slings.
There is no trade association, nor is there a formal industry standard covering, for hydraulic gantry design, manufacture, testing, or use. Therefore, all aspects of these machines are subject to the judgment of manufacturers and riggers.
Relative FAQ
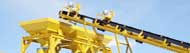
- Telescopic crane
- Crushing Plants
- Aerial Working Platform
- Self-erecting crane
- Drilling machine
- Screening Machine
- Tunnel Boring Machinery
- Hobbing Machine
- Slimming Machine
- Bulldozer with Hydraulic Scraper
- Track Mobile Plant
- Dedusting & ash conveying
- Blast resistant doors
- E-energy Breast Beautifying Laser
- Electric dust collector
Email: sales@bossbuyer.com
Skype: bossbuyer
Market Hotline
0086-21-61435-919
Service Hotline:
0086-21-61435-919