Jacking Towers
Jacking towers are used primarily for vertical movement of large loads in tight quarters or out-of-the-way locations where a large crane may not be suitable. There are two well-established types: those which push the loads up can be called push-jack systems, and others which pull from above are strand jack systems.
A typical jacking tower is a frame supported on a foundation and perhaps guyed for stability. Towers may be triangular or rectangular in cross section. A tandem pair is usual, but four towers can be utilized if needed. The towers can be braced or guyed to one another.
The push-jack system uses a crossbeam from which the load is suspended, hence towers must always be taller than the load. The crossbeam in turn is suspended from yokes which climb within guide slots built into the near legs of each tower, a pair of hydraulic jacks at each end pushes the beam up until a locking plate, or dog, can be inserted and support the load. With the crossbeam safely seated, the jacks can be retracted in preparation for the next increment of climbing. Thejacks are short and remain in place; climbing is accomplished by inserting solid-steel lifting pistons each time thejacks are retracted. Between strokes, previously placed lifting pistons rest on the dog. There are twojacks located at the base of each tower; the lifting pistons are inserted, and the lock plates are located at the base of the towers. Thus, all climbing work is accomplished from the ground.
Advantages of push-jack systems are that they are rudimentary and thus easily understood and repaired, provide positive load guidance, and can be worked from the ground. Disadvantages are that they are slow, lack means for lateral adjustment, and the guys must be assiduously watched and maintained.
A strand jack system requires suspending loads from framing at the tower tops; the framing can be concentrically supported by the towers or may be supported on the inboard tower legs. Slings or lifting bars are attached to the load and run up to a lift beam. The lift beam is fitted to receive the lifting tendons which are typically a bundle of 18-mm- diameter high-strength wire-rope strands selected to satisfy load weight.
The lifting tendons go up to strand jacks mounted on the overhead cross beam (really a pair of beams or trusses). The center-hole strand jacks pull up the tendons stroke by stroke, gripping them forjack retraction and repeating the cycle as needed. At the start, as the jacks begin to extend, the upper grippers grab the tendons by means of friction and wedging forces. At the end of the stroke, the jacks are reversed and the lower grippers are similarly engaged; after this, the upper grippers are released. After full retraction, the cycle is repeated. Withdrawn tendon material is spooled. The power pack powering thejacks is normally located at top as well.
A pair of towers can support one or two point picks. Four towers can be used for either two or four point lifts. In the four-tower arrangement, a crossbeam is employed to support each pair of load-supporting jacks, and header beams support the crossbeam (or beams). As heavy loads are often supported near the center of the pair of headers, these are commonly robust members. A four-tower setup can be self-bracing; this eliminates the need for external guys. The savings in guys and deadnien, however, would probably be exceeded by the costs of shipping and erecting two extra towers, header beams, and rigid bracing members. Therefore, a four-tower arrangement would only be used when dictated by advantage or necessity such as when the load must be shifted laterally or the lift is from four points. When two towers are used, they may have to be anchored to a substantial moment-resisting footing or would need guys to restrain wind and side loading during the operation as shown in Figure 2.48. If the towers are guyed, the guys should be preloaded because of the base fixity. Preloaded guys imply larger deadmen for anchorages than passive guys.
Strand jacking offers precise control over the load. A system can also be configured to provide for transverse and longitudinal load movement, even rotation, for precise placement, but these features come at added cost. For loads of common magnitude, chain falls can be used to pull the load into final alignment. If sufficient drift height has been provided, pulling forces are not very large and can be easily accommodated, but the designer must allowed for this in advance.
Although jacking equipment is at the top of the towers, controls and instrumentation can be on the ground. Pressure and stroke data for each jack (including guy preload jacks) can be continuously metered and can show up in readouts at an instrumentation station. One control lever operates thejacks and a second lever operates the gripper hydraulics. Jacks can be operated singly or simultaneously, speed can be varied as well. However, with the mechanical action taking place at the top, including spooling of excess strand, it would be prudent for someone to be at the top to verify that equipment is functioning properly. TV cameras can also be considered for that purpose (Figure 2.49).
Though good synchronization requires reliable instrumentation, the strand jack method has a track record of accomplishing many difficult heavy lifts. During the lift, the load is always held in the grippers when static, and on the center-hole jacks when in motion.
Strand-jack system advantages are
- Precise vertical load control and the ability to correct for lateral out of plumbness by operating onejack
- Control and monitoring from the ground
- High load capacity utilizing simple towers that can break down into small sections
- Moderately fast operation, with typical loads being able to be lifted within a normal work day
- Adjustable guys that can readily correct alignment and out of plumbness to within tolerance even as the system changes from the unloaded to loaded condition
Relative FAQ
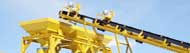
Email: sales@bossbuyer.com
Skype: bossbuyer
Market Hotline
0086-21-61435-919
Service Hotline:
0086-21-61435-919