Limiting Tower Crane Operator Fatigue
Operators and contractors both benefit from 72-hour seat policy
When operators sit in a tower crane cab for 16 hours a day, a lot may go through their minds—and the longer they sit there, the more distracted they may become. Combine that with the constant radio chatter and directions given by the signalperson, and operators will no doubt become mentally tired and fatigued.
Dennis Kenna, president of Heede Southeast, and I began to study the habits of our tower crane operators. When contractors were allowed to work the operators double-time—80 or 90 hours a week—we began to notice that they became mentally strained after sitting in the cab for as little as 65 hours per week. Although they were not physically tired because they had been sitting all day, this mental weariness affected our operators levels of alertness, leading them to make mistakes in the seat. Although no accidents occurred, the potential safety hazards were enough for our company to implement a 72-hour in-the-seat policy, which limits the time our in-house operators can spend in the tower crane.
The positive effects of tracking time
Keeping track of the time spent in the seat is fairly simple. Every week, the jobsite superintendent has to review and approve the operator’s timesheet. When the supervisor scans in and emails the timesheet, Heede’s safety department records the hours for the week. Our operators know that if they are working more than 72 hours or getting close to meeting the cap, I will put in a relief operator for a day or two while they rest.
While we were not sure what type of reaction to expect from our operators when we implemented the 72-hour seat policy a year and a half ago, we have seen a tremendous change in their attitudes. They have called and thanked us for putting this policy in place because contractors can no longer work them as long as they want. Site superintendents also have found that the operators are more agreeable. Even their spouses have taken notice of the positive effect the fewer hours has made on their attitudes (and the fact that they are home more).
Contractors also see the benefit of limiting hours in the operator’s seat. Prior to this policy, some contractors would try to keep operators in the cab for as many as 24 hours straight—and they were willing to pay the overtime just to keep them working. But just because the operators aren’t physically fatigued does not mean this is a safe practice. By keeping them to a 72-hour schedule, there has not only been a turnaround in near-misses but also in operators returning to the project on time and alert. Additionally, we’ve found this policy to be less expensive for the customer. They now realize it is cheaper for them to pay a second operator and have two work shifts than one operator working a 24-hour shift on overtime. Plus, they have an alert operator in the seat at all times.
In a recent example, we had a contractor in Raleigh-Durham who wanted an operator to bypass the 72-hour work policy. When I approached him about it, his attitude was that if he was paying for the operator, the operator was going to work the hours that he wanted. I explained Heede’s policy and how he is actually saving money by bringing in a second operator. He realized that not only is this to his benefit, but also the site will be safer with a fresh operator. Heede has, in turn, hired more crane operators to meet the new company requirements.
We employed this policy to improve safety within Heede’s operation and have discovered the payoff goes beyond protecting our people and equipment. We’ve seen a big turnaround in near-misses, alertness, and operators’ attitudes. If your company is experiencing safety issues, I would suggest you look at where your site safety is lacking. How many hours are your operators working, and how much time off do they have between shifts? It may be time to develop your own hours-in-the-seat policy.
Relative FAQ
- Tower Crane Superstructure
- Tower Crane For Sale
- Topless Tower Crane For Sale
- Self-Raising Tower Crane
- Limiting Tower Crane Operator Fatigue, Operators and contractors both benefit from 72-hour seat policy
- Introduction of overhead crane operator
- Safe Crane Operations
- Question About Tower Crane - 3
- Walking Crane For Operation By Power Or Hand
- Wind and Tower Cranes
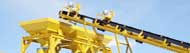
Email: sales@bossbuyer.com
Skype: bossbuyer
Market Hotline
0086-21-61435-919
Service Hotline:
0086-21-61435-919