FAQ >> Crane accessories and auxiliary equipment
Crane accessories and auxiliary equipment
End truck
- Maximum strength by using a rigid box-section design with reinforced connection areas as well as machined tolerances in the crane girder connection system guarantee superior structural integrity and optimum travel characteristics with minimum wear
- The precise travel wheel alignment and exact adaptation of the crane span dimension via interchangeable spacer elements ensure optimum travel characteristics and high adaptability
- End trucks confi gured with proprietary structural design programs
Power supply line
- Demag DCL compact conductor line for 4 to 7 poles; connections ensure long-term power supply and minimize unplanned downtime
- Pre-assembled building blocks for simple assembly or replacement of current collector trolleys or complete straight sections provide optimum serviceability
- IP 23 or IP 24 high protection against accidental contact with sealing lip and integral expansion joints for optimum safety
Travel unit
- Maintenance-free drives with anti-friction bearings lubricated for life, maximum bearing centers to accommodate horizontal forces, and travel wheels made of spheroidal graphite nodular iron provide for favorable travel characteristics and minimum crane runway wear
- Infi nitely stepless variable travel speeds via frequency inverters with speeds up to 240 fpm guarantee travel with minimum load-sway as well as precise positioning
Hoist trolleys
- State-of-the-art Demag DR rope hoist of C-shaped design optimized for crane applications with higher hoist and cross travel speeds provides higher handling rates and effi ciency for cranes with capacities up to 50 m t
- Compact designs with minimum approach dimensions and larger hook path guarantee optimum utilization of the available space and height and reduce initial construction and subsequent costs
- Infi nitely variable hoist and travel motions guarantee low-sway handling. Precise, gentle positioning provides for greater safety and convenient operation
- CAN Bus technology to meet tomorrow’s demands for high data transmission reliability, corresponding to safety class 3 to DIN / EN 954, ensures optimum monitoring for greater effi ciency thanks to preventive maintenance
Control system
- Ergonomically designed control units for safe, fatigue-free handling. The display provides complete transparency for control of the installation. The CAN Bus control system corresponds to safety category 3 to DIN / EN 954.
- Demag DSE pushbutton control pendant suspended for separate travel on the crane girder
- Handheld or belly box CAN Bus radios for wireless control allow operator fl exibility
Bottom block
- Enhanced bottom block design with standard load hook for ease of load connection
- Rope lead-in guard eliminates the risk of being caught between the rope and sheave
- Handle recesses on both sides simplify handling of the bottom block and increase operating safety
Relative FAQ
- Crane Safety, Crane Quality Control
- Crane machine history, Crane history
- Truck Crane Standard Carrier Equipment
- Tower Crane Carrier, Crane Carrier
- Crane Control program analysis and comparison
- Rule about crane brakes and restraints
- Rough Terrain Crane Boom Equipment
- Construction Machinery Types and Applications
- Bridge and gantry cranes
- YJCrane Gantry Crane
Relative Products
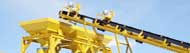
- Diode laser equipment
- RF Beauty Equipment
- Beauty Spa Equipment
- Water and Oxygen Jet Machine
- Bulldozer with Blade and Ripper
- E-energy Breast Beautifying Laser
- Electrical discharge machining
- Forestry farvester
- Sand Washing Machine
- Roll Crusher, Roll Mill
- Gyratory Crusher
- Track Mobile Plant
- Fire Rated Steel Door
- Pulse bag dust collector
- Air box pulse dust collector
Contact Us
Email: sales@bossbuyer.com
+ encranechina@hotmailh�u�o�j[8�h9��_!�tkgo6�O�
�
44�[sr�чԍ?(�@f.+j��x�!ԝ��z1?D$q0�#�R����#>)~Њ�(]~�}j��)(szQ5fr-�
�=0��$b�6&��a � k�<���y�n|:�? �O