Crane Control program analysis and comparison
In recent years, updating and development of bridge crane in order to improve crane performance as the main indicator, the speed of which the most prominent crane. The following are several commonly used to speed the program cranes were analyzed and compared. 1. Speed ??rotor resistance (1) cam controller to control the rotor resistance asymmetry of the program used for 5 ~ 10t bridge crane of the main control circuit common, through the tandem asymmetric rotor resistance, the inherent characteristics of the motor speed curve to achieve the purpose. This simple structure, low cost, but the speed varies greatly, the middle-speed instability. Strictly speaking, the program can not be referred to as speed, it can only improve the motor starting characteristics. (2) The master controller to control the motor speed single-phase and reverse decline The program used for general-purpose 1 6 ~ 50t bridge crane control circuit, which is characterized by reversible asymmetric circuit. Increase in tandem with each block starting motor rotor resistance; down the first block to reverse braking, only to return in the first block by the second block when the work, and the load must be greater than the rated load of 56; down the second block is Single-phase braking, mainly for light load down; down the third block as regenerative braking. The program structure is simple, low cost, but can not increase speed, mechanical properties of very soft, great rate of speed change, speed is not a long run. 2. Exciting force from the brake speed Circuit is characterized by reversible asymmetric circuit, down three-phase AC motor disconnect power to the two-phase stator winding leads to the formation of the early air-gap magnetic field excitation current, the motor load in the potential of cutting the air gap under the rotor magnetic field, induced current and braking torque. Rectified and then into the stator windings, so that increased air-gap magnetic field excitation current enhanced braking torque increases. Braking torque equal to the potential energy load torque acting on the motor shaft, the rotor current, self-excited current remained constant, stable operation of the motor. When you change the rotor resistance, the motor speed changes, the equivalent of cranes rises and Series Resistance Starting Rotor speed. The program falls in heavy, with medium-speed and high-speed gear, energy saving and more reliable. But the rise can not be a stable low-speed, light load can speed, the operation is not convenient. 3. Hydraulic plunger speed Rotor speed access via electric transformer putting hydraulic brake motor stator, rotor voltage and frequency for motor with its speed and change, so when the motor speed increases, the rotor voltage and frequency reduced accordingly, reduced power f is also reduced thrust hydraulic brake braking torque corresponding increase brake, the motor speed decreased. On the contrary, the motor speed down to reduce the braking torque, the motor speed increases. When the load torque, variable torque and braking force generated by the motor torque balance, and stable operation of the motor to achieve speed control purposes. Access the program through high value of rotor resistance, the system rise and fall may be more stable low speed. But it can only get a low, intermediate-speed characteristics of the soft, and must make changes to the mechanical parts of the crane can be used. 4. Eddy Current Brake Speed Motor and eddy current brake coaxial link, when the motor speed falls off the motor, eddy current brake power. Brake gate opening, load down, this time issued eddy current brake braking torque. When the load torque and eddy current brake braking torque equilibrium, the load decreases the low-speed stable. Motor speed falls in the middle of the reverse power condition, the field winding eddy current brake power, man-made systems are the motor torque characteristics and the synthesis of eddy current brake curve. When the load torque and the torque balance synthetic motor speed when the speed dropped back down} braking. Rise in the positive electric motor to run the state, the governor is basically the same principle and falls. The program rise and fall can be speed, speed ratio of up to 1: lO, the middle-speed, low speed can be obtained. But the speed is changed greatly, not the middle-speed long-running, more complex circuits, we must make changes to the mechanical parts of the crane can be used. 5. The stator voltage control thyristor Three-phase power per phase series motor into a group of anti-parallel thyristors, by changing the thyristor conduction angle, to control the motor stator voltage and to achieve speed. Speed ??range up to 1:10 this scenario, the speed change rate of less than 5, can speed up and down, with some prospects. But the program more complex, debugging difficult. 6. Frequency AC variable speed frequency control is the speed in the ideal solution, but using the crane is still rare, mainly because the crane starting torque; crane fall in energy regenerative braking when the motor state; drive higher prices, etc. caused by reasons. With the progress of science and technology, large-scale integrated circuit technology, computer technology, PWM technology, vector conversion technology and energy feedback technology has been successfully applied in the inverter, the inverter used in the crane has been mature. (1) Work Such as the photo shows, the starting contactor pull KM energized, the drive is energized, the signal indicator light DM, R, s frequency separation of control power and main circuit wiring, circuit protection action in order to keep the drive abnormal output signal, ease of maintenance and failure analysis. SA master controller turned up a gear when, K3, K5 pull, drive forward the signal STF, low-speed signal SD RL terminals connected with the public. Then there are start-frequency output inverter, the motor does not rotate. Because the brake does not open, but not enough to avoid starting torque slip hook, K1 zero protection and disconnect the abnormal output protection (drive B, C contacts the abnormal output contacts). When the output frequency of 3Hz brake release when the frequency setting, and the maintenance of the brake release current detection setting 0.3s asked, the inverter output terminals will be required by RUN to open the brake. SE RUN terminal and pass the lead, K8 was electric contact is closed. K9 suction units, brake motor M2 is energized. STOP terminal connected with the SD at the same time protect themselves. Brake motor energized and opened, the braking time is 0.3s, the drive to the start 3Hz frequency drive motor began to turn. Frequency of the drive continuously variable speed up time to the set value, can be seen hoisting crane speed change is also continuous. With the SA from low gear to high gear switch. K5, K6, K7 state were combined into seven different input frequency, so that the output of seven different frequencies to obtain the lifting speed of seven different stops, SA through the block back to zero, the inverter output frequency in the deceleration time continuous decrease. When the output frequency is equal to the frequency of cervical braking closed (6Hz) time. Mechanical brake signal through the RUN terminal are closed. SE RUN and open, K8, K9 off, STOP with the SD terminal off, brake start closing. Drive through O. 5s after the stop output, M1 motor to stop. Rise down the same principle and principle of frequency control loop drawings (2) performance characteristics Magnetic flux vector control frequency conversion technology with high torque or upgrade their skills, solve the crane starting torque, low speed high torque output and strong giant load change problem; acceleration and deceleration settings when asked, solve the crane system moving the impact of changes in the speed of the crane continuous, smooth operation; use of the frequency detection signal reaches the control frequency signal or open and close the brake, only the motor output torque is greater than the load torque, the brake was opened to address the slide hook problem using power feedback technology to run the motor in the fourth quadrant of renewable energy conversion back into the 50Hz AC power, protecting the drive is not breakdown; main control loop separate and reliable ground to avoid the strong current of the weak signal of the thousands of scratch drive . Frequency is the best option crane speed one, speed ratio up to 1:10 or more, can realize stepless speed regulation. Mechanical properties of the gear speed is very hard, heavy start-up and stable and reliable low-speed, acceleration and deceleration time settings so that each block starts and stops at a fairly steady. With high control precision, the design is faulty display, analysis and parameter monitoring capabilities, easy to use and maintain, and easy to realize automatic control and remote control.
Relative FAQ
- Brakes, Controls, Derricking Jibs and Cabins for Operators of Cranes
- Crane Rigging a Load and Crane Overloading
- Crane accessories and auxiliary equipment
- Construction Machinery Types and Applications
- Crane Wire Rope Replacement Criteria - What is bad rope?
- YJCrane Gantry Crane
- Rule about crane brakes and restraints
- Gantry Crane or Goliath Crane
- Crane Preventive Maintenance Checklist
- Crane Gantry
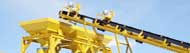
- Blast resistant doors
- Crusher Loaders Dumpers
- Construction Scrapers
- Tracked Carriers
- Dedusting & ash conveying
- CO2 Fractional Laser
- Electric dust collector
- Forestry farvester
- Water and Oxygen Jet Machine
- Gas Tight Doors
- Hammer Crusher, Hammer Mill
- Air box pulse dust collector
- Pulse bag dust collector
- Track Mobile Plant
- EOT Crane
Email: sales@bossbuyer.com
Skype: bossbuyer
Market Hotline
0086-21-61435-919
Service Hotline:
0086-21-61435-919