Electric Hoist Failure Analysis and Treatment
In recent years, the use of electric hoist to install the increasing volume of production, the gourd is also increasing the number of failures, which not only affects the production of the normal operation of a major accident will lead to serious and how to reduce or prevent accidents, improve electric hoist the safe operation of timely and accurate processing of various fault occurred in operation, has become an important part of the production. The following combination of experience in installation and maintenance company, to hoist some of the common causes of failure of concrete analysis. 1, by starting electric hoist does not work after the switch Mainly due to the hoist rated voltage not connected, but unable to work, there are 3 general situations: (1) whether the electric hoist power supply system power transmission, usually by Shi Dianbi tests, such as did not get electricity, and other transmission after work; (2) hoist the main, the electrical control circuit is damaged, broken or bad line , also will hoist motor can not power, such a situation, to be the main repair, control circuit, repair, in order to prevent the main, three-phase motor control circuit to give the power phase and burning motor, or the operation of hoist motor suddenly energized , harm, be sure to hoist the motor is disconnected from the power lines, only to master, control circuit power transmission, and then switch to move the start and stop to check the electrical and control circuits of the work on the problem of electrical or line repair or replacement, as confirmed Lord, trouble-free control loop, before re-testing; (3) the hoist motor terminal voltage is lower than 10% of rated voltage, the motor starting torque is too small, so do not moving cargo lifting hoist, and can not work, check with a multimeter or voltage meter and other measuring motor input voltage is indeed due to low voltage, the motor can not be started, the need to return to normal after system voltage such as using electric hoist. Sometimes, the hoist motor voltage is normal, while the hoist is not working, it must consider other factors, such as: motor is burned, the motor should be replaced when maintenance; hoist long-term need, poor maintenance and other reasons for the brake wheel and cover because of rust, starting not open when the brake wheel off, the motor only to issue a "hum" sound, do not turn up, hoist not work. At this time, should remove the brake wheel, cleaning the surface rust and then re-test; Motor serious sweep chamber, but also make the motor does not rotate, that this situation should stop using the motor must be overhauled or replaced to ensure the hoist work . In addition, the production of Do not overload the use of electric hoist, when the goods are too overloaded, fixed cargo crane hoist, the motor only issued a "hum" sound, not running, and in severe burning of the motor, or even cause the accident, then immediately shut down, reduce the goods, so that work at rated power gourd. 2, electric hoist abnormal noise when running Many electric hoist failure, such as control of electrical appliances, motor or reducer failures, often accompanied by abnormal noise, the noise level and sound location and cause of the fault do not differ on, repair, we should hear and see more, sound can be characterized by or under the failure to determine the issue of sound location, find and repair faults. (1) abnormal noise occurred in the control loop, issued a "hum" noise, usually a fault contactor (AC contactor, such as bad contact, the voltage level does not match the core was stuck, etc.), should fault contact with devices for maintenance, not repair must be replaced, treatment, elimination of noise themselves. (2) an abnormal motor noise, should be immediately shut down, check whether the motor running single phase, or bearing failure, coupling axis errors and the "sweep bore" and other failures, which will cause abnormal motor noise, the sound of different fault location and the level and the sound difference, single-phase operation, the motor issue regularly suddenly strong suddenly weak, "buzzing" sound; and bearing damage when the bearing near the issue along with "Ko Deng - Ko Deng," the "buzz" sound; the coupling axis is not correct, or the motor bore a slight sweep the whole issue of high electrical "buzzing" sound from time to time along with the shrill voice. In short, the difference should be based on the noise, find the fault, the itemized repair and restore the normal performance of the motor when the motor failed when untreated, prohibit the use of gourds. (3) abnormal noise from the gear issue, gear failure (such as lack of gearbox or bearing oil, gear wear or damage, bearing damage, etc.), then should stop to check, first determine the reducer or gear box bearings added prior to use oil, whether used oil changed regularly, such as lubrication is not required, will not only produce high gear, "buzzing" sound, but also excessive wear or damage to the gears and bearings. Some people think that without a temporary or casual gear add a little oil, can still run, not a serious fault, such thinking is wrong. I installed an electric hoist time, but had forgotten the workers to gear box oil injection, just try one day, high noise reducer that is issued to open the gear box, find gear for excessive wear and obsolescence. Bearing damage reducer, and motor bearing failure similar to, but also in the vicinity of an abnormal bearing noise. In order to prevent the failure to expand, regardless of excessive wear or damage to the gear reducer or gear bearing damage, needs immediate repair or replacement of demolished, eliminating failure, reduce the noise. 3, the braking distance of more than fall down requirements Long-term disabled electric hoist, it was wrong to adjust the brake adjusting nut, or excessive brake ring wear, the brake spring pressure decreases, reducing the braking force, when the shutdown, the brake is not reliable, down from more than requirements, As long as this statement by hoist requirements, you can re-adjust the brake nut. But the work should be noted that lifting heavy weights, the Prohibition of adjustment, brake inspection and maintenance. Sometimes, adjusting the brake nut, slipped down from the still exceeds the requirements, encountered such a situation, we must consider other reasons, first, we open the brake ring, check the brake surface is sticky oil, such as a sticky oil , friction coefficient decreases, when the brake will slip, down from more than the requirements, only a little use to adjust the brake nut, then only wash the brake surface (clean-to-use light petrol) to restore braking surface friction coefficient ; Secondly, as the brake ring loose or damaged, can not guarantee an effective brake brake ring, only the replacement of brake ring; sometimes found brake ring is not damaged, only after the brake ring and cone cover bad when braking braking surface contact is too small, the braking force is too small, so that fell from more than requirements, maintenance, in order to increase the braking force, should find out the location of poor contact, the grinding, increases the contact surface when braking, no grinding, the need to replace parts; hoist motor coupling traverse not working or stuck, shut down, the brake ring and the cone after the end cap is bad or can not reach, so that the braking effect gourd good times and bad, such cases, the coupling should overhaul or replacement. In addition, the brake pressure spring fatigue long-term use, so that smaller spring force, shut down, the brake is not solid, you should replace the spring, re-adjust the braking force. 4, the motor temperature is too high Should first check whether the overloading of hoist use, overloading lead to motor heating, long-term overload will burn the motor; motor is not overloaded, still hot, check the motor bearing is damaged; should also check whether the requirement to work the motor system of work, which is caused by motor heat One of the reasons, the use of work system should be in strict accordance with the motor work. The motor running, brake gap is too small, not completely torn off and have a great friction, the friction heat at the same time equivalent to the additional load, the motor speed is reduced, the current became larger and the heat, and you should stop working, re- adjust brake clearance. 5, weight rose to the air, can not start after stopping Analysis of the reasons, first check whether the system voltage is too low or fluctuate too large, the case of this situation, such as the voltage returned to normal only after the start; the other hand, pay attention to phase three-phase motor in operation, can not be started after the shutdown, At this point need to check the power phases. 6, can not stop or to limit the location is still not stopping Such cases are generally contactor contact welding, when the press stop switch, contactor contact can not be disconnected, the motor was electric as usual operation, hoist does not stop; to the limit as limit the location of faulty hoist is not parking. This happens, immediately cut off the power to make gourd to stop. Parking, maintenance, or limit access to devices, severely damaged beyond repair and must be replaced. 7, gear oil Reducer oil leakage due to: (1) between the gear box and the lid, seal assembly of non-performing or failure damage, repair or replace the seals should be removed; (2) did not tighten the screw gear link, the shutdown , should tighten the screws. 8, bore brush motor Generated because the sweep chamber: severe wear on the motor shaft support ring, the rotor core displacement, or for other reasons that the stator core displacement, causing the motor rotor and stator gap is too small conical scanning chamber occurred. Motor is prohibited "sweep bore," after the event bore brush, remove the support ring should be replaced, adjust the gap between the stator and rotor cone to make even, or to the repair station for repairs. Electric hoist on the analysis of common faults and handling, so that maintenance personnel to deal with failure gourd, know where to start checking, improve maintenance efficiency, in addition, for operators to provide on-site processing problems.
Relative FAQ
- Rule about crane brakes and restraints
- Brick Making Machines: Features, Uses and Types
- Crane Control program analysis and comparison
- Rule about marking rated capacity of crane
- Metals, cement, and aggregates crusher development
- Use of aggregates for asphalts around the world
- Electric Overhead Travelling Crane (EOT Crane) Parts
- Security requirements for crane hooks
- Mast Style Jib Crane
- Classification of Crane Anti-sway devices
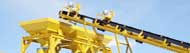
- Electrical discharge machining
- Electric dust collector
- Electric Wheel Loader
- Diode laser equipment
- Telescopic crane
- Bulldozer with Blade and Ripper
- Caterpillar Equipment
- Er:bium Glass fractional laser
- E-energy Breast Beautifying Laser
- Water and Oxygen Jet Machine
- Roll Crusher, Roll Mill
- Dedusting & ash conveying
- Fire Rated Steel Door
- Long Pulse ND:YAG Laser
- Hammer Crusher, Hammer Mill
Email: sales@bossbuyer.com
Skype: bossbuyer
Market Hotline
0086-21-61435-919
Service Hotline:
0086-21-61435-919